200 Jahre Zink in Stolberg
Berichtet von Friedrich Holtz im Mai 2020
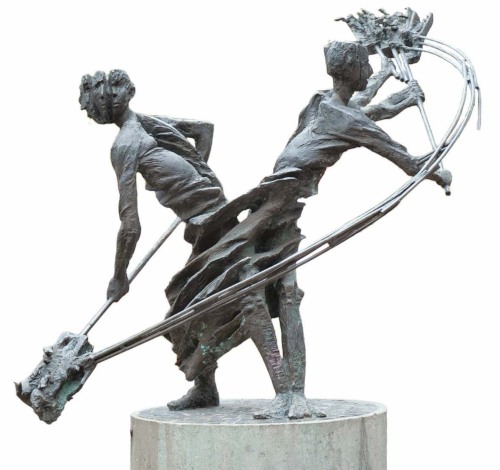
Skulptur eines Zinkschmelzers von Prof. Hennig Seemann, Foto: B. Engelen.
In Stolberg begann die Geschichte der
Zinkindustrie 1819 mit dem Bau einer Zinkhütte durch Matthias
Leonhard Schleicher auf dem Gelände seines Kupferhofes Velau.
Wenig später, nämlich 1820, also vor genau 200 Jahren, waren
mit der Einführung des Zinkwalzens alle Voraussetzungen zur
großtechnischen Herstellung von Zinkprodukten aller Art gegeben.
Die eingangs erwähnte Zinkhütte
Velau (erbaut 1819) wurde 1837 vom Eschweiler Bergwerksverein
übernommen. Darüber hinaus entstanden in Stolberg drei
weitere Zinkhütten, nämlich die von der Stolberger
Gesellschaft betriebene Zinkhütte Münsterbusch (1834), die
zur Eschweiler Gesellschaft gehörende Zinkhütte Birkengang
(1845) sowie die Zinkhütte Steinfurt (1850). Letztere allerdings
war nur etwa ein Jahrzehnt in Betrieb.
|
Zinkhütte
Birkengang,
Lithographie von Adrien Chanelle,
Bilder bitte anklicken !!! |
Die 1834 - 37 von John Cockerill erbaute
Zinkhütte Münsterbusch wurde bis 1967 betrieben. Um die Mitte
des vorigen Jahrhunderts wurde in der Zinkhütte Münsterbusch
eine Muffel mit ovalem Querschnitt entwickelt, welche Rheinische Muffel
genannt wurde. In Zinkhütten, die mit liegenden Muffeln
arbeiteten, fand dieser Muffeltyp später weltweit Verwendung. Das
der Hütte angeschlossene Zinkwalzwerk blieb noch bis Ende
März 1991 in Betrieb. Das Schwungrad des damaligen
Walzwerkantriebes befindet sich heute als Freilichtexponat in der
Außenanlage des Zinkhütter Hofes.
|
Foto: F, Holtz |
Wie eingangs erwähnt, hatte man 1820,
also nur ein Jahr nach der Errichtung der Zinkhütte Velau, mit der
großtechnischen Produktion von Walzzink begonnen und
spätestens bis 1860 hatten insgesamt vier Zinkwalzwerke ihren
Betrieb aufgenommen. Diese Betriebseinrichtungen lieferten Zinkbleche,
die ihrerseits eine Massenproduktion von korrosionsbeständigen
Haushaltswaren ermöglichten. Ob Putzeimer, Gießkannen,
Badewannen u.v.a.m. wurden aus gewalztem Zinkblech hergestellt.
|
Foto: F, Holtz |
Ebenfalls auf Grund der guten
Korrosionsbeständigkeit fand Zink auch im Baugewerbe weite
Verbreitung. Dachrinnen und Regenfallrohre beispielsweise werden auch
heute größtenteils aus Zink hergestellt. Bis zur Mitte des
20. Jahrhunderts fand Zinkblech häufig und insbesondere an der
Wetterseite von Gebäuden als Fassadenverkleidung Verwendung.
.
|
Haus Loh
Foto: F, Holtz |
Ein gutes Beispiel hierfür ist Fassadenverkleidung von Haus Loh an
der Zweifaller Straße. An diesem um 1900 entstandenen Bauwerk
sind historistische Bauelemente (Tudor Revival) noch deutlich
erkennbar. Zum Thema Historismus und zu den in Stolberg hergestellten
Zinkornamente wird
weiter unten noch ausführlich berichtet.
Die Zinkhütten-Industrie im früheren Stolberg sowie deren
Entstehung, Entwicklung und Bedeutung wäre ohne die hiesigen
Erzlagerstätten nicht vorstellbar gewesen. Deshalb scheint es
angebracht, kurz über die damalige Bergbausituation in Stolberg
und Umgebung zu berichten.
Von den insgesamt etwa zehn Stolberger Erzabbaugebieten: Breinigerberg,
Brockenberg, Burgholz, Büsbacherberg, Diepenlinchen,
Glücksburg, Hammerberg, Herrenberg (Verlautenheide), Kirchfeld-
Heidchen (Eilendorf) und Römerfeld (zwischen Gressenich und Werth)
belieferten insbesondere die Gruben Breinigerberg und Diepenlinchen die
Stolberger Zinkindustrie mit Erzen. Die Grube Breinigerberg wurde nach
kriegsbedingten Unterbrechungen (Kriegsjahre 1870/71), 1883
endgültig aufgegeben. Die Grube Diepenlinchen in Mausbach hingegen
stand zwischen 1890 und 1910 in bester Entwicklung und erreichte
Spitzenwerte von mehr als 10 000 Jahrestonnen.
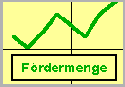
Skizze: F. Holtz, nach DUNKEL, F.
(1989) Kapitel 7 u. RÜBMANN, A. (1925)
Als kurz nach dem 1. Weltkrieg die Mausbacher Erzgrube Diepenlinchen
1919 auf Grund von Problemen mit der Wasserhaltung (Entwässerung
der Grubenbaue) ebenfalls geschlossen wurde, wurden die Stolberger
Zinkhütten mit Erzen aus Bergwerken beliefert, die
zwischenzeitlich von der Gesellschaft für Bergbau, Blei- und
Zinkfabrikation zu Stolberg übernommen worden waren.
|
Schalenblende, ein polymetallisches Erz,
Sammlung und Skizze: F. Holtz |
In der zweiten Hälfte des 19. Jahrhunderts setzte der
königlich-preußische Baumeister Karl Friedrich Schinkel
erstmalig Zink als Gestaltungselement in der Architektur ein. Diese
Elemente waren teilweise als reine Ornamentik, teilweise jedoch auch
als figürliche Darstellungen in Reliefform oder Vollplastik
ausgeführt. Hiermit leitete Schinkel einen geradezu weltweiten
Modetrend ein, denn die Verwendung von Zinkornamentik als
Dekorations-Accessoire in der Architektur erfreute sich bald
allgemeiner Beliebtheit. Die Stil- und Formenfülle kam
insbesondere dem Geltungs- bzw. Repräsentationsbedürfnis des
in der Gründerzeit reich gewordenen Bürgertums entgegen.
Die Architektur des ausgehenden 19. Jahrhunderts war in hohem
Maße durch die Nachahmung historischer Baustile geprägt.
Insbesondere Romanik, Gotik und Klassizismus dienten als
nachahmenswerte Vorbilder. Zur begrifflichen Differenzierung der
nachempfundenen Architektur setzte sich allgemein die Verwendung der
Vorsilbe "Neo" durch. Der zeitgleiche Stilpluralismus, zusammenfassend
auch mit dem Begriff Historismus belegt, erforderte ein
variantenreiches Sortiment von Dekorationselementen wie
Dachaufsätze, Gesimse, Skulpturen, neogotisches
Fenstermaßwerk, Wetterfahnen, Ecktürmchen, Balustraden etc.,
die unter Verwendung des korrosionsbeständigen Zinks relativ
einfach herzustellen waren.
Zinkornamente im Museum Zinkhütter Hof, hergestellt von
Kraus, Walchenbach & Peltzer Ende 19. Jahrhundert.
(bitte anklicken)
Bei der Herstellung der Statuetten und
Skulpturen bediente man sich zunächst des klassischen Formgusses,
wobei entweder die erforderlichen Einzelteile mittels Metallformen
gegossen und später zusammengelötet wurden oder das gesamte
Gussteil durch den Einsatz "verlorener" Sandformen entstand.
Von besonderer Bedeutung war der sogenannte Zinksturzguss. Eine aus
mehreren Teilen zusammengesetzte Stahlform wurde mit flüssigem
Zink gefüllt. Nach wenigen Sekunden, wenn das flüssige Zink
an der kühlen Formoberfläche zu erstarren begann, wurde die
Form so gedreht (gestürzt), dass das im Innenbereich flüssig
gebliebene Zink durch die Einfüllöffnung wieder
abfließen konnte. Somit entstanden gegossene Hohlkörper,
deren Außenseite exakt der gewünschten Geometrie entsprach.
Dieses Verfahren eignete sich hervorragend zur
Großserienfertigung und erlaubte auf Grund der entstehenden
Hohlkörper einen sparsamen Materialeinsatz und gewährleistete
somit auch ein relativ geringes Gewicht der Gussteile. Letzteres war
durchaus von praktischer Relevanz, wenn man bedenkt, dass mit diesem
Verfahren großvolumige, lebensgroße Skulpturen hergestellt
wurden.
.
|
Flora, römische Göttin des Frühlings, Zinkguss gefasst. |
Eine im Zinkhütter Hof befindliche Skulptur der Flora
(römische Göttin der Blumen und Feldfrüchte) vermittelt
die perfekte Illusion von behauenem Stein. Insbesondere die monochrome,
sandfarbene Fassung gibt der Skulptur die Anmutung einer alten,
verwitterten Steinmetzarbeit.
Bei der Anwendung des Zinksturzgussverfahrens ließen sich bei den
gegossenen Hohlkörpern nicht beliebig dünne Wandstärken
erreichen. Bei kürzeren Verweilzeiten des Zinks in der Form, also
beim frühen Stürzen, reduzierten sich zwar die
Wandstärken, jedoch erhöhte sich hierdurch auch die Gefahr,
dass sich Fehlstellen bildeten und die gegossene Skulptur Löcher
aufwies.
Dünne und gleichmäßige Wandstärken konnten bei
einer anderen Fertigungsmethode erreicht werden. Hierbei lötete
man die Skulptur aus einer Vielzahl von tiefgezogenen und entsprechend
geformten Zinkblechen zusammen. Bei der Planung und Auslegung der
einzelnen Blechteile wurden deren Konturen so festgelegt, dass
möglichst unauffällige Nahtstellen entstanden. Vorzugsweise
verliefen die Lötnähte z.B. entlang eines Faltenwurfs in der
Bekleidung, entlang des Haaransatzes oder auch entlang des
Halsausschnittes.
.
|
Victoria, die
Siegesgöttin,
Zinkblech. |
Technologische Besonderheiten
Zinkverhüttung
Die Herstellung von Zink ist erst seit Anfang des 19. Jahrhunderts
möglich, nachdem die hierfür erforderliche, anspruchsvolle
Technologie, die Zinkdestillation, entwickelt worden war. Die
Schwierigkeiten bei der Herstellung von Zink ergaben sich aus dem
Umstand, dass bei der Verhüttung nicht flüssiges Zink
(Siedepunkt 907
oC),
sondern Zinkdämpfe entstanden, die sich überdies bei Kontakt
mit Luftsauerstoff zu staubförmigem Zinkoxid umwandelten. Dieses
Problem wurde dadurch gelöst, dass man die entstehenden
Zinkdämpfe in sogenannten Muffeln unter Luftabschluss
kondensierte.
Die Zinkdämpfe, die sich zusammen mit Kohlenmonoxid in der Vorlage
angesammelt hatten, konnten hier kondensieren, weil besagte Vorlage aus
dem eigentlichen Feuerraum des Ofens herausragte und somit kühler
gehalten wurde (Zink: Siedepunkt 907oC, Schmelzpunkt 420oC). Die der
Muffel abgewandte Seite der Vorlage war mit einer
röhrenförmigen Öffnung versehen, durch die das
Kohlenmonoxid abströmen konnte, wodurch das Eindringen von
Luftsauerstoff in das Muffelsystem verhindert wurde. Beim Austritt aus
der Vorlage wurde dieses Kohlenmonoxid sofort abgefackelt und zu
Kohlendioxid aufoxidiert. Dieser exotherme Vorgang heizte das ohnehin
schon heiße Gas noch weiter auf, sodass schwach leuchtende
Flammen entstanden. Mit dem Abfackeln des austretenden Gases vermied
man nicht nur eine Ausbreitung des höchst toxischen
Kohlenmonoxids, sondern die Erscheinungsform der Feuerzungen erlaubte
den Zinkschmelzern auch Rückschlüsse auf den Fortgang des
Verhüttungsprozesses.
.
|
Anordnung von Zinkmuffeln in einem Zinkofen, Foto: F. Holtz. |
Besonderheiten beim Walzen von Zink
Eine weitere Eigenart bezieht sich auf das Walzen von Zink. Hierzu
erstellte das Freilichtmuseum Hagen (Lutz Engelskirchen) ein
bemerkenswertes Traktat, welches 2006 publiziert wurde. Besagte
Besonderheit ergab sich daraus, dass dieses Metall nur innerhalb eines
Temperaturbereiches von etwa 100 bis 200
oC geschmeidig und
somit walzbar war. Unterhalb und erstaunlicherweise auch oberhalb
dieses Temperaturbereiches ist das Material so spröde, dass es
sich nicht plastisch verformen lässt. Diese abnorme
Materialeigenschaft des Zinks ist seit etwa 1805 bekannt.
.
|
Zinkwalzwerk
Freilichtmuseum Hagen
Foto: F. Holtz. |
Fernerhin wird durch das Walzen des Zinks die Korn- und Gitterstruktur
so verzerrt, dass sich im gewalzten Zinkblech eine unerwünschte
und äußerst unangenehme Eigenschaft einstellt. Bei Anwendung
des üblichen Walzverfahrens war Zinkblech nämlich stark
anisotrop, d.h.: es stellten sich in Walzrichtung deutlich andere
Verarbeitungseigenschaften ein als quer zur Walzrichtung.
Das Problem der Anisotropie wurde dadurch gelöst, dass bei den
einzelnen Walzdurchläufen das Walzgut um jeweils 90o gedreht wurde
(kreuzweises Walzen). D.h.: der jeweils nachfolgende Durchlauf (auch
Stich genannt) erfolgte quer zu der Walzrichtung des vorherigen
Durchlaufes. Zur Beschleunigung des Fertigungsablaufes und zur besseren
Handhabung des Walzgutes wurden nicht einzelne Zinkbleche gewalzt,
sondern man arbeitete üblicherweise nach dem sogenannten
Paketwalzverfahren (gleichzeitiges Walzen mehrerer übereinander
gelegter Zinkbleche).
Da Reversierwalzwerke (umkehrbare Drehrichtung) nur mit erheblichem
konstruktiven Aufwand realisierbar waren, mussten die Pakete nach jedem
Durchlauf um das Walzengerüst zur Einlaufseite zurück
transportiert werden, um dann erneut in den (zwischenzeitlich enger
gestellten) Walzenspalt eingeführt zu werden.
Das immer wieder neue Einführen des Blechpaketes in den enger
gestellten Walzenspalt führte zu Laststößen, die das
Antriebsaggregat kaum hätte abdecken können. Somit wäre
das Wasserrad zum Stillstand gekommen. Dies wurde bei wassergetriebenen
Walzwerken häufig durch den Einsatz von wuchtigen
Mühlrädern vermieden, deren rotierende Massen als
Energiespeicher dienten und, ähnlich wie ein Schwungrad, den
kurzfristig und schlagartig erhöhten Energiebedarf abdecken
konnten.
|
Wasserrad des Zinkwalzwerkes,
Foto: F. Holtz. |
Diese Anlage befand sich ursprünglich auf dem Betriebsgelände
der Firma Hoesch in Schneidhausen bei Kreuzau. Besagte Familie
gehörte zu der aus Stolberg stammenden Eisenhütten-Dynastie.
Mittlerweile ist das komplette Zinkwalzwerk vom Freilichtmuseum Hagen
übernommen und dort wieder originalgetreu aufgebaut worden.
Zunächst kann man sich aus heutiger Sicht eigentlich nur wundern,
wieso die Stolberger Zinkindustrie im etwa 20 km entfernten
Schneidhausen ein Zinkwalzwerk betrieb. Hierbei ist zu bedenken, dass
die Erzeugung von mechanischer Antriebsenergie nur mit
Wasserrädern und Fließgewässern möglich war,
welche ein hinreichendes Gefälle aufwiesen. Die aus der Eifel
kommende Rur wies im Vergleich zu Stolbergs Bächen (Vichtbach,
Inde, Wehe) eine erheblich höhere Wasserführung auf.
Somit war der Standort Schneidhausen im Rurtal damals auch für die
Stolberger Zinkindustrie höchst attraktiv. Die Verfügbarkeit
von Energie verbesserte sich erst, als 1905 der Urftsee gebaut war und
mit der Inbetriebnahme des Jugendstil-Kraftwerkes Heimbach mit der
Elektrifizierung unserer Region begonnen wurde.
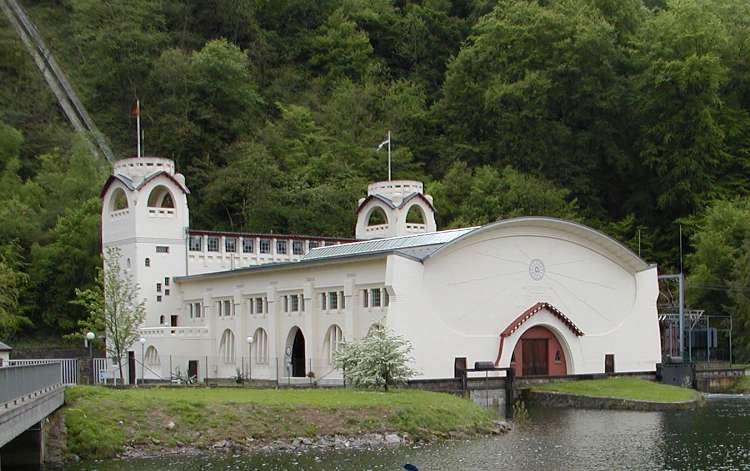
Jugendstil-Kraftwerk Heimbach, Foto:
Rureifel-Tourismus.